О. А. Юланов, В. В. Леснов, В. М. Гладченко, И. В. Леснов, А. В. Гладченко
КОМПЬЮТЕРНЫЙ КОНТРОЛЬ АВТОМАТИЧЕСКИХ СИСТЕМ РЕГУЛИРОВАНИЯ
Статья в журнал "Электрические станции"
Технический контроль состояния сложных промышленных систем регулирования всегда представлял собой серьезную научную и инженерную задачу. В частности, автоматические системы регулирования (АСР) турбоагрегатов, обеспечивающие надежное и эффективное управление турбинами тепловых станций представляют собой сложные и многокомпонентные системы, от исправного состояния которых зависит безопасность эксплуатации тепловых электростанций и качество электрической энергии.
До настоящего времени большинство АСР турбин испытывается без использования современных средств автоматизации. При этом применяемые методы контроля, реализуемые согласно "Методическим указаниям по проверке и испытаниям автоматических систем регулирования и защит паровых турбин" ОРГРЭС (МУ 34-70-062-83, ОРГРЭС, Москва, 1991 г.), в достаточной мере совершенны и предусматривают полные испытания АСР. К сожалению, на основе "старых" понятий реализация этих методик при испытаниях дает в большинстве случаев недостаточно объективные оценки, так как в этих случаях используются органолептические методы [1].
Например, статическая характеристика турбины снимается и строится органолептическим методом с помощью физических лиц - наблюдателей, расставляемых по точкам измерения и записывающих данные по общему (обычно звуковому) сигналу. Далее эти данные обрабатываются руководителем испытаний. Характеристика в виде графика строится вручную. Подобный метод построения статической характеристики определяет ее недостаточную точность (погрешность может достигать 10%) и обуславливает субъективность оценок состояния турбоагрегата. Этим самым создаются условия для необъективной оценки результатов проведенных промежуточных ремонтов и наладок регулирования турбин, что в отдельных случаях приводит к серьезным авариям.
Несмотря на очевидные недостатки указанных методов контроля, даже приказ РАО ЕЭС "О повышении качества первичного и вторичного регулирования частоты электрического тока в ЕЭС России" № 524 от 18.09.2002 предусматривает только подобные испытания [2].
Это следует из текста соответствующего пункта Приложения 1 к указанному приказу [2].
"2.8. В каждом опыте с помощью регистрирующих приборов или наблюдателями вручную должны быть зафиксированы:
- моменты нанесения возмущающих воздействий и их фактическая величина;
- за 3 мин до нанесения возмущения и в течение всего переходного процесса до стабилизации режима:
- активная мощность турбогенератора энергоблока; суммарная мощность всех работающих турбогенераторов очереди ТЭС (или каждого в отдельности);
- давление пара перед турбиной энергоблока; в общем паропроводе ТЭС;
- минимальное и максимальное содержание кислорода (02) в дымовых газах (по штатному регистратору);
- параметр, характеризующий положение регулирующих клапанов турбины энергоблока при работе в зоне скользящего давления.
Каждый опыт должен заканчиваться стабилизацией активной мощности на новом уровне, восстановлением исходного значения давления свежего пара в опытах при номинальном давлении или стабилизацией давления на новом уровне в опытах при скользящем давлении.
Регистрацию переходных процессов можно производить автоматически или вручную с обязательной фиксацией момента нанесения возмущения. Для автоматической регистрации целесообразно использовать многоканальные самопишущие приборы с непрерывной записью (например, типа Н-327 или их аналоги, осциллографы и т.п.), многоточечные (печатающие) регистраторы, а при наличии ИВС или АСУ ТП - специально сформированные протоколы с последующей распечаткой на принтере или графопостроителе" (Приложение 1 к приказу РАО "ЕЭС России" от18.09.2002 № 524 "Временные методические рекомендации по проверке готовности ТЭС к первичному регулированию частоты в ЕЭС России").
Некоторые виды испытаний не могут проводиться при использовании "ручных" методов снятия характеристик. К таким видам испытаний относятся, например, измерения времени перемещения органов регулирования из-за краткосрочности процессов. Современная техника, и в частности компьютерная и микропроцессорная техника позволяют не только выполнять подобные испытания, но и в значительной мере автоматизировать процесс испытаний турбин и снятие характеристик состояния АСР. Этим обеспечивается получение объективных данных состояния АСР, сокращается риск пропуска возможных отклонений параметров, уменьшаются трудозатраты на проведение испытаний, сокращается необходимое время проведения испытаний.
Это в совокупности дает значительную экономию средств, что достигается полной автоматизацией снятия характеристик и использованием компьютерных методов обработки результатов испытаний. Пример оценки эффективности применения компьютерных систем контроля приводится далее.
Цель настоящей статьи - познакомить эксплуатационный персонал электростанций с объективным способом проведения испытаний АСР турбин с помощью компьютерной системы контроля (КСК). В статье специалистам-наладчикам будет представлен достаточный технический материал для оценки качества проведения контроля АСР с использованием такой системы.
Испытания турбин проводят в несколько этапов, на каждом из которых получают необходимую и достаточную информацию для дальнейшей диагностики состояния турбины. В том числе до начала ремонта и после его завершения проводят статические испытания на остановленной турбине, целью которых является получение данных о состоянии силовых элементов АСР и, на основе диагностического анализа, получение сведений о требующемся объеме ремонтных работ и/или качестве выполнения ремонта. В частности, данные, получаемые в итоге испытаний, используются для построения характеристик, которые могут быть сопоставлены с формулярными (паспортными) характеристиками завода-изготовителя, что и отражает действительное состояние турбины.
При успешном завершении испытаний на остановленной турбине с использованием того же оборудования проводят испытания АСР при работе турбины на холостом ходу (статические испытания), а также испытания при импульсном изменении нагрузки (динамические испытания). В каждом виде этих испытаний используют наборы датчиков, с помощью которых контролируют работу соответствующих узлов АСР. Перечисленные виды испытаний проводятся в разные интервалы времени и функционально между собой не связаны, однако данные с предыдущих этапов контроля используются при подготовке и планировании испытаний последующих этапов [3, 4].
При проведении полных испытаний АСР, включающих испытания на остановленной турбине, испытания на турбине, работающей на холостом ходу и под нагрузкой, а также импульсные испытания и испытания АСР полным сбросом электрической нагрузки, с использованием КСК обеспечиваются измерения следующих параметров:
- перемещение кнопки защитного устройства (ЗУ);
- перемещение механизма управления турбиной (МУТ), промежуточных золотников, золотников регулятора скорости и регулятора давления, золотника электрогидравлического преобразователя;
- перемещение серводвигателей, поворотных заслонок;
- угол поворота кулачкового вала регулирующих клапанов;
- давление рабочей жидкости в линиях АСР и защиты, в полостях серводвигателей;
- давление свежего пара, пара в регулирующей ступени, в камерах регулируемых отборов, перед регулирующими клапанами и за ними, давление перед частью среднего давления (после промежуточного перегрева);
- частоту вращения ротора турбины и частоту электрической сети;
- уровень вакуума в конденсаторе.
Кроме того, по желанию заказчика КСК-4 можно обеспечить измерение других физических параметров, используя не только набор датчиков разработки ЗАО "Теплоэнергетические технологии", но и любых других датчиков (в том числе и с использованием штатных датчиков турбоагрегата), имеющих унифицированный выходной сигнал, принятый в КСК-4.
Первоначально при создании компьютерной системы контроля предполагалось с помощью КСК проводить испытания только по снятию статической характеристики регулирования. Однако при проработке вопроса стало очевидно, что все виды испытаний проводимых на АСР тесно взаимосвязаны. Поэтому оказалось нецелесообразным внедрять в практику компьютерный метод только для снятия статической характеристики и оставлять все остальные испытания по-прежнему органолептическими ("ручными"). Это справедливо, поскольку разработанная программно-аппаратная база и имеющиеся разнообразные датчики позволяют автоматизировать практически все необходимые испытания.
Система КСК разрабатывалась в течение ряда лет. Она продолжает совершенствоваться и в настоящее время является эффективной и надежной системой контроля состояния АСР тепловых турбин. Программное и аппаратное развитие КСК привело к созданию современной компьютерной системы, позволяющей оперативно и качественно проводить весь комплекс требуемых испытаний АСР при снятии статических и динамических характеристик систем регулирования паровых турбин в условиях эксплуатации. На сегодня система выпускается в четвертой модификации и получила обозначение КСК-4. Кроме этого типа создана модификация КСК - 4 для проведения вибродиагностики и вариант для проведения тепловых испытаний (КСК-4/ТИ) [4].
Для обеспечения мобильности системы контроля, необходимой в связи с разновременностью проведения разных этапов контроля, она реализована с использованием портативного персонального компьютера типа NoteBook. Применение портативного персонального компьютера не является самоцелью. В системе КСК-4 в принципе может быть применен любой другой компьютер класса не ниже Р4 или использован модуль-накопитель разработки ЗАО "Теплоэнергетические технологии", размещаемый при испытаниях вблизи турбоагрегата (ТА). Вся обработка данных при любом исполнении КСК-4 может проводиться в другом помещении на стационарном или другом персональном компьютере.
Система КСК выполнена таким образом, что она может быть смонтирована за 1,5 - 2 часа двумя исполнителями на объекте испытаний и также быстро демонтирована. Для других испытаний (например, при снятии параметров тепловых расширений ТА) возможно "стационарное" размещение КСК (с использованием модуля-накопителя информации), предполагающее снятие характеристик в течение 7 - 10 суток при непрерывном контроле.
Особенностью системы КСК-4 является также и то, что при наличии полного соответствующего набора датчиков все виды испытаний после завершения ремонта ТА могут быть проведены за один проход без переустановки датчиков и без какой-либо специальной подготовки КСК. Благодаря этому общее время контроля сокращается в несколько раз при получении объективной и полной информации о состоянии ТА. Получаемые данные не зависят от индивидуальных особенностей персонала станции, проводящего эти испытания. Этим обеспечивается объективность контроля.
Система КСК-4 может быть использована наладочным и ремонтным персоналом электростанций и наладочных организаций при испытаниях гидравлических, электрогидравлических и других типов систем регулирования, при вибродиагностике, при балансировке роторов ТА в собственных подшипниках. Вид испытаний планируется при их подготовке. Этим определяется необходимое количество и состав датчиков. В КСК-4 имеется возможность накапливать, систематизировать и хранить информацию по всем каналам измерения в памяти компьютера или на магнитном диске. Из управляющего компьютера информация может быть перенесена на другие совместимые с IBM компьютеры для последующего накопления, архивирования, обработки и так далее.
В систему КСК-4, помимо компьютера со специальной программой, входят устройство преобразования (УП КСК), источник питания (ИП), а также набор кабелей и датчиков, необходимых для снятия характеристик турбины. Номенклатура датчиков и кабелей, качество и уровень программного обеспечения КСК-4 позволяют организовать практически любые виды испытаний АСР турбин. За счет применения программных методов тарировки датчиков и специальных программ обработки данных рассматриваемая система КСК-4 является высокоинтеллектуальным программно-аппаратным комплексом, все части которого могут совершенствоваться независимо друг от друга. Это позволяет постоянно совершенствовать всю систему в целом.
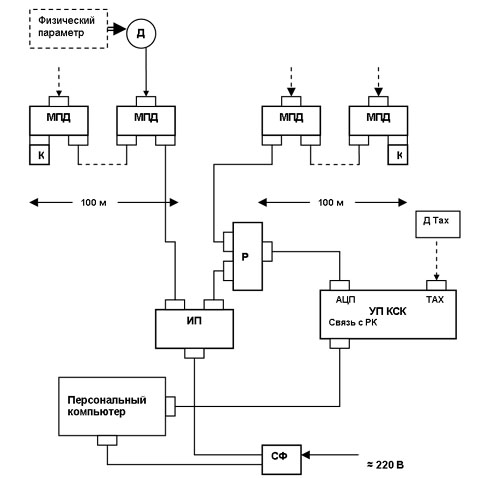
Функциональная схема КСК-4 представлена на рисунке 1. В ней приняты следующие сокращения:
Д - датчик физического параметра для преобразования физического параметра в электрический сигнал стандартизованного диапазона;
Д Тах - датчик тахометрический (для контроля частоты вращения турбины);
МПД - модуль подключения датчика для согласования усилителя датчика с интерфейсом системы;
Р - разветвитель для формирования двунаправленного интерфейса;
СФ - сетевой фильтр для подавления помех сети питающего напряжения;
АЦП - вход аналого-цифрового преобразователя для преобразования токового сигнала в цифровую форму;
ТАХ - вход тахометрический для ввода сигнала от тахометрического датчика;
К - коннектор (заглушка) для согласования линии связи МПД-УП КСК.
В схеме указан только один датчик (Д). Другие датчики подключаются аналогично. Каждый датчик содержит масштабирующий усилитель, обеспечивающий формирование стандартизованного токового сигнала в диапазоне 0 - 5 мА, значение которого соответствует в определенном масштабе значению физического параметра. Усилители датчиков через модули подключения датчиков (МПД) объединяются в единую аналоговую магистраль, по которой обеспечивается ввод информации от датчиков на вход УП КСК. При этом суммарная длина линии связи может достигать 200 м (по 100 метров в обе стороны относительно места расположения компьютера или модуля-накопителя информации).
В УП КСК осуществляется аналого-цифровое преобразование сигналов для их ввода в персональный компьютер (РС). По сигналам управления от РС в соответствии с программой каждый датчик опрашивается через МПД индивидуально в течение порядка 100 мксек. Благодаря такой организации линии связи "датчик-компьютер" обеспечивается высокое быстродействие работы всей системы. В качестве датчиков используются, как правило, датчики разработки ЗАО "Теплоэнергетические технологии", хотя возможно использование и других типов датчиков, имеющих стандартизованный токовый выход. Такие датчики подключаются, как правило, через специальное устройство гальванической развязки (УГРА), обеспечивающее гальваническую развязку по принципу "аналоговый сигнал - аналоговый сигнал".
Для установки датчиков на объекте испытаний используются специально разработанные приспособления с магнитными "присосками", что обеспечивает простоту установки датчиков и возможность быстрой сборки системы на объекте. Общее количество датчиков для контроля физических параметров в системе КСК-4 может быть до 256 каналов и более. На практике при испытаниях АСР турбин обычно общее количество каналов контроля не превышает 32, но при необходимости количество каналов измерения может наращиваться.
Необходимо сказать также, что КСК-4 может быть использована не только для контроля параметров АСР в процессе испытаний ТА (мобильное, или временное развертывание), но и при эксплуатации ТА в штатных режимах (стационарное размещение). В этом случае будут регистрироваться все параметры ТА во всех технологических режимах работы. Поскольку в этом случае вся информация о работе каждого узла АСР будет выводиться на БЩУ, персонал станции будет иметь оперативную информацию о состоянии ТА в целом. Это будет повышать качество и надежность эксплуатации ТА за счет оперативного выявления возможных отклонений в режимах работы узлов и систем ТА. Безусловно, при стационарном размещении КСК необходимо обеспечить стационарное размещение датчиков. Кроме того, должна быть такая прокладка кабелей КСК, при которой будут исключены возможные случайные обрывы или расстыковки кабельных соединителей.
Для снятия и контроля характеристик АСР, как правило, используются следующие типы датчиков (типовой набор):
- перемещения (положения) с диапазоном измерения 30, 50, 200 и 300 мм;
- угла поворота с диапазоном измерения до 360О;
- наклона с диапазоном измерения ± 20 угл. мин.;
- давления тензометрические с диапазоном от 1 кг/см2 до 1000 кг/см2;
- вибрации;
- оборотов (фотодиодные и/или индуктивные).
При работе с системой КСК-4 при снятии характеристик системы регулирования от эксплуатационного персонала электростанции требуется наличие минимальных навыков работы с персональным компьютером. Анализ снятых характеристик позволяет проводить диагностику состояния узлов и систем турбины.
В системе КСК-4 предусмотрены следующие основные режимы работы:
- "Таблица распределения каналов (ТРК)", предназначенный для закрепления датчиков за определенными измерительными каналами КСК;
- "Тарировка", используемый для точного назначения датчикам пределов измерения и получения корректировочного графика: "показания образцового прибора-показания канала измерения"; данный режим позволяет объективно повышать точность измерения параметров, недостижимую при иных методах контроля;
- "Осцилографирование", предназначенный для записи контролируемых величин в память компьютера и на его твердый магнитный диск;
- "Графика", обеспечивающий формирование необходимых зависимостей между контролируемыми величинами. Этот же режим необходим и для вывода этих зависимостей на экран моСЊСЋ. Р’ системе РљРЎРљ-4 РІ принципе может быть применен любой РґСЂСѓРіРѕР№ компьютер класса РЅРµ РЅРёР¶Рµ Р 4 или использован модуль-накопитель разработки Р—РђРћ "Теплоэнергетические технологии", размещаемый РїСЂРё испытаниях вблизи турбоагрегата (РўРђ). Р’СЃСЏ обработка данных РїСЂРё любом исполнении РљРЎРљ-4 может проводиться РІ РґСЂСѓРіРѕРј помещении РЅР° стационарном или РґСЂСѓРіРѕРј персональном компьютере.
Система КСК выполнена таким образом, что она может быть смонтирована за 1,5 - 2 часа двумя исполнителями на объекте испытаний и также быстро демонтирована. Для других испытаний (например, при снятии параметров тепловых расширений ТА) возможно "стационарное" размещение КСК (с использованием модуля-накопителя информации), предполагающее снятие характеристик в течение 7 - 10 суток при непрерывном контроле.
Особенностью системы РљРЎРљ-4 является также Рё то, что РїСЂРё наличии полного соответствующего набора датчиков РІСЃРµ РІРёРґС‹ испытаний после завершения ремонта РўРђ РјРѕРіСѓС‚ быть проведены Р·Р° РѕРґРёРЅ РїСЂРѕС…РѕРґ без переустановки датчиков Рё без какой-либо специальной подготовки РљРЎРљ. Благодаря этому общее время контроля сокращается РІ несколько раз РїСЂРё получении объективной Рё полной информации Рѕ состоянии РўРђ. Получаемые данные РЅРµ зависят РѕС‚ индивидуальных особенностей персонала станции, проводящего эти испытания. Ртим обеспечивается объективность контроля.
Система РљРЎРљ-4 может быть использована наладочным Рё ремонтным персоналом электростанций Рё наладочных организаций РїСЂРё испытаниях гидравлических, электрогидравлических Рё РґСЂСѓРіРёС… типов систем регулирования, РїСЂРё вибродиагностике, РїСЂРё балансировке роторов РўРђ РІ собственных подшипниках. Р’РёРґ испытаний планируется РїСЂРё РёС… подготовке. Ртим определяется необходимое количество Рё состав датчиков. Р’ РљРЎРљ-4 имеется возможность накапливать, систематизировать Рё хранить информацию РїРѕ всем каналам измерения РІ памяти компьютера или РЅР° магнитном РґРёСЃРєРµ. Р |